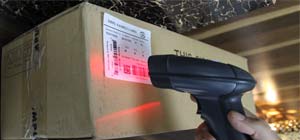
Guide to Implement Barcode Scanning Systems for Packaging
By providing comprehensive training, hands-on experience, documentation, regular refresher training, and encouraging feedback, packaging workers can become proficient in the use of barcode scanning systems and improve their efficiency and accuracy.
Posted By:Tech Solution | Last Updated On:
Staff Training Steps To Use Barcode System
Packaging workers can be trained to use barcode scanning systems effectively and efficiently by following these steps:
-
Comprehensive Training:
Provide comprehensive training to workers on how to use the barcode scanning system. The training should cover the basics of barcode technology, how to read and scan barcodes, and how to use the scanning software.
-
Hands-on Training:
Provide hands-on training to workers by allowing them to practice scanning different types of barcodes and packaging materials. This can help them to become more familiar with the barcode scanning system and how it works.
-
Use of Documentation:
Provide workers with documentation that outlines the scanning procedures, including how to troubleshoot common problems that may arise during scanning. This can help workers to be more efficient and minimize errors.
-
Regular Refresher Training:
Provide regular refresher training to workers to ensure that they stay up-to-date with the latest technology and techniques for scanning barcodes.
-
Provide Incentives:
Provide incentives to workers who demonstrate consistent compliance with barcode scanning policies and procedures. This can help to encourage a culture of compliance and improve the effectiveness of the system.
-
Monitor Compliance:
Monitor compliance with barcode scanning policies and procedures through regular audits and feedback from workers. Corrective action should be taken if any deviations from the policies and procedures are identified.
-
Encourage Feedback:
Encourage workers to provide feedback on the barcode scanning system, including any issues they encounter, suggestions for improvement, or ideas for new features. This can help to improve the effectiveness of the system and ensure that it meets the needs of the workers and the organization.
By following these steps, packaging companies can ensure that their workers are trained to use barcode scanning systems effectively and efficiently, and that they comply with the company's policies and procedures related to barcode scanning.
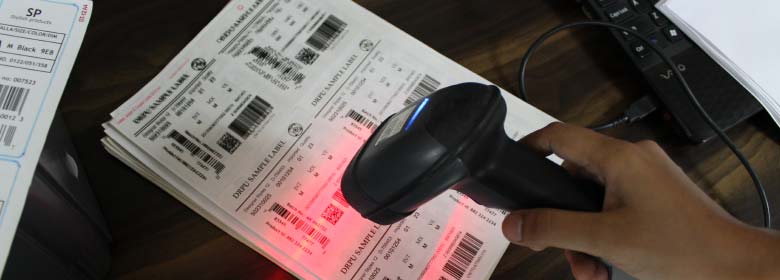
Integration of Packaging Barcode Systems With Other Packaging IT Systems
Packaging barcode systems can be integrated with other packaging IT systems such as inventory management and order tracking by using software and hardware that allow for the exchange of data between systems. The following steps can be taken to integrate barcode systems with other packaging IT systems:
Need of Integrated system: |
Identify the packaging IT systems that need to be integrated with the barcode system, such as inventory management and order tracking systems. |
Choose Compatible Software and Hardware: |
Choose software and hardware that are compatible with both the barcode system and the other packaging IT systems. This may involve selecting software that can import and export data in the required format, and hardware that can connect to multiple systems. |
Configure the Systems: |
Configure the barcode system and the other packaging IT systems to ensure that they can communicate with each other. This may involve setting up data exchange protocols, configuring network connections, and testing the integration. |
Develop Data Exchange Protocols: |
Develop data exchange protocols that specify how data will be exchanged between the barcode system and the other packaging IT systems. This may involve developing scripts or code to automate data exchange, or manually exporting and importing data between systems. |
Train Personnel: |
Train personnel on how to use the integrated systems, including how to scan barcodes, how to access and update inventory information, and how to track orders using the integrated systems. |
API Integration: |
Application Programming Interfaces (APIs) can be used to connect barcode systems with other IT systems. This allows for data to be shared between systems in real-time, which helps to ensure that inventory levels and order statuses are always up-to-date. |
Middleware Integration: |
Barcode systems can be integrated with middleware, which can then connect with other IT systems, such as inventory management and logistics systems. |
Cloud-Based Integration: |
Cloud-based barcode systems can be integrated with other cloud-based IT systems using web services. This allows for data to be shared between systems in real-time and can be especially useful for companies that have multiple locations. |
Custom Integration: |
Companies can develop custom integrations between their barcode systems and other IT systems. This can be done using various programming languages and tools, but requires more technical expertise than other integration methods. |
Monitor and Maintain The Systems: |
Monitor the integrated systems to ensure that they are functioning correctly and that data is being exchanged accurately. Regular maintenance and updates may be required to ensure that the systems remain compatible and effective. |
Overall, integrating barcode systems with other IT systems can help packaging companies streamline their operations and improve efficiency. By automating data entry and eliminating manual processes, companies can reduce errors, save time, and improve accuracy.
Improvement in Efficiency and Accuracy in Package Delivery by Courier Company Barcode Systems
Courier company barcode systems improve efficiency and accuracy in the processing and delivery of packages by providing a standardized way of identifying and tracking packages throughout the delivery process. Here are some ways that barcode systems help:
-
Package Tracking
Barcode systems allow courier companies to track the location and status of packages at every stage of the delivery process. As packages move through the system, they are scanned at various checkpoints, allowing the company to see exactly where a package is at any given time.
-
Sorting
Barcode systems can help automate the sorting process by allowing packages to be scanned and sorted automatically by destination. This can save time and reduce errors that can occur when sorting is done manually.
-
Verification
Barcode systems also provide a way to verify the accuracy of package information. The barcode on each package contains key information such as the recipient's name and address, so when a package is scanned, the system can check that the information matches what is in the courier company's database.
-
Delivery Confirmation
When a package is delivered, the barcode on the package is scanned, providing proof of delivery and allowing the recipient to track the package's delivery status in real-time.
-
Time-Saving
Barcode systems save time by eliminating the need for manual data entry. Instead, information is automatically entered into the system when the barcode is scanned, reducing the risk of errors and increasing efficiency.
Overall, barcode systems play a crucial role in improving efficiency and accuracy in the processing and delivery of packages for courier companies, providing benefits for both the company and its customers.