Varnish v/s laminate : Which Label Coating is Good for Your Products?
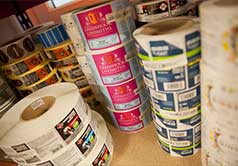
We find that many users either don’t know or are confused about the choice of label coating for their labels. Have you ever had to choose between varnish and laminate coating finishes for your labels? Trying to choose between the right material, finish, and adhesive may seem quite tricky at the beginning. This guide will help you decide on that. Varnish and laminate can also boost the visual appeal of your product label with a smoother, glossier finish, and you should avoid topcoating if you want a more natural look with texture and no shine.
Why Coating?
A coating is designed to protect a product label from damage by scuffing or friction during its useful working life. Paper labels also need an extra protective coating of either varnish or lamination to protect against moisture or general wear. These specialist coatings can come in several surface finishes, including gloss, matte, glitter, sensory applications, etc., and are used to highlight specific areas of a design by using spot varnish techniques.
Varnish Label Coating
The varnish protective coating seals the ink and the label from common damage. A varnish coating is easy to apply and gives a relatively longer lifespan than just paper labels. Based on your requirements, apply varnish over the custom-printed labels to seal both gloss and matte finishes. Varnishes help protect against scuffs and abrasions. It typically costs less than laminates, but they don’t hold up as long.
Laminate-coated Labels
Laminates are ideal for labels that will be exposed to moisture, abrasion, and light. It is the gold standard of label protective coatings and some experts in the industry consider the laminate coating the ultimate protection. Laminates also protect against scuffing, but will better prevent smearing from oils and other agents. The coating is available in a thin bi-oriented polypropylene film or Thermal Transfer polyester that’s applied after printing to seal and protect the ink.
Advantages of Varnish and Laminate Labels
Varnish Labels
- Varnishes give a more professional appearance to a quality paper stock.
- A varnish will enhance the print and stock of the label it is added to.
- Varnish labels protect against the moderate scuffing and smudging.
- Varnishes are typically cheaper than lamination label and give a smooth finish to custom label, allowing it to have a consistent texture.
Laminate Labels
- Lamination provides an added layer of protection to product labels.
- If you have a label that will be exposed to oils or liquids, a laminate will better protect the quality of your label.
- It cheapens the look of the label as it gives it a plastic-like appearance.
- To show off the aesthetic characteristics of the paper stock, lamination may not be the best choice for that.
Which one is best for your Labels?
This depends on what you're looking for from your custom labels, like look, feel, and durability. You may need either option to meet your needs. Both of these finishes use different application techniques for the protection of custom labels and add an aesthetic appeal to the product. If your product labels don’t need a longer lifespan and do not expose too much moisture and you are concerned about eco-friendliness, go for varnish labels.
If you want to ensure minimal creases and for packaging to sustain tough environments, lamination is the better option. To maximize shelf life, aesthetics, and longevity over sustainability, it is possible with lamination label coating.
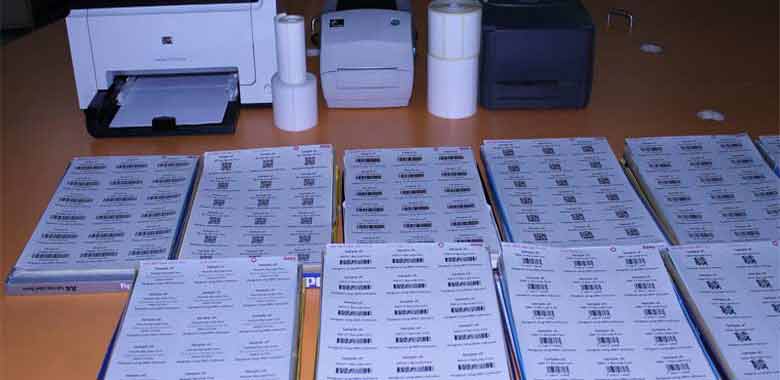
Future of Barcode Technology in Distribution
The future of barcode technology in distribution is very promising, as it has the potential to significantly improve the efficiency and accuracy of the distribution industry. Here are some examples:
-
Real-time tracking: Barcode technology can be used to track products in real-time, allowing distributors to monitor their products as they move through the supply chain. This can help to identify any bottlenecks or issues in the supply chain and allow for timely intervention.
-
Improved inventory management: Barcode technology can be used to track inventory levels in real-time, allowing distributors to keep track of their stock levels and avoid stockouts or overstocking.
-
Enhanced picking accuracy: Barcode technology can be used to improve picking accuracy in warehouses, reducing errors and improving overall efficiency.
-
Streamlined logistics: Barcode technology can help to streamline logistics, enabling distributors to optimize their delivery routes and reduce transportation costs.
-
Better customer service: Barcode technology can help to improve customer service by providing customers with accurate delivery estimates and allowing them to track their orders in real-time.
How will this Barcode Technology continue to improve the Distribution Industry?
Overall, the future of barcode technology in distribution is likely to involve further integration with other technologies such as artificial intelligence, the Internet of Things, and blockchain. This will enable distributors to optimize their operations even further, improving overall efficiency and customer satisfaction.
Additionally, the increasing adoption of mobile barcode scanning technology is making it easier for distributors to scan barcodes on the go, reducing the need for stationary barcode scanners and increasing the flexibility of barcode scanning in the distribution industry.