Introduction of Courier Company Barcodes
A courier company barcode is a unique identifier code assigned to packages and parcels to facilitate their tracking and management within a courier or delivery system. The barcode contains information about the package, such as the sender's address, the recipient's address, the delivery service level, and the tracking number. It can be scanned by a barcode scanner to retrieve this information.
The courier company barcode system works by assigning each package a unique barcode. When a package is picked up by the courier, it is scanned and the information is recorded in the courier company's database. This allows the courier company to track the package as it moves through the delivery network, from pickup to delivery.
Download and Install Barcode Software
Information of Courier Company Barcodes
-
Code 128
Code 128 barcodes are used to label and track packages as they move through the courier company's system. This barcode system can encode a large amount of information, such as package destination, sender information, reciever information, delivery instructions, and many more.
-
QR Code
QR codes are becoming increasingly popular in the courier industry as a way to provide customers with easy access to package tracking information. By scanning the QR code with a mobile device, customers can quickly and easily see the status of their package and track its progress.
-
PDF417
PDF417 barcodes are used in the courier industry to encode large amounts of information, such as shipping labels and customs documentation. This barcode system is often used for international shipments, where customs documentation is required.
-
Data Matrix
Data Matrix barcodes are used to label and track small packages, letters, and envelopes. This barcode system can store a large amount of data in a very small space, making it useful for tracking packaging items or products with the limited labeling space.
Ensuring the Accuracy and Quality of Barcode Information by Courier Company Workers
Courier company workers can ensure the accuracy and quality of the information encoded in barcodes by following these steps:
-
Verify the Accuracy of the Barcode
Before scanning the barcode, ensure that the barcode label is clear and free from damage or smudging. If the barcode is damaged, it may not scan accurately, leading to errors in tracking and delivery of the package.
-
Verify the Information in the Barcode
After scanning the barcode, check the information displayed on the scanner to ensure that it matches the information in the database. Any discrepancies should be investigated and resolved to prevent errors and delays.
-
Scan the Barcode Correctly
Hold the scanner perpendicular to the barcode and at the appropriate distance to ensure that the barcode can be accurately scanned. The scanner should emit a beep to indicate a successful scan.
-
Properly Handle the Package
After scanning the barcode, handle the package with care to ensure that it is not damaged during transport. Proper handling can also help ensure that the package is delivered to the correct location.
By following these steps, courier company workers can ensure the accuracy and quality of the information encoded in barcodes, which can help improve the efficiency and reliability of the delivery process.
Integration of Courier Company Barcode System with other IT System
Courier company barcode systems can be integrated with other courier IT systems such as package tracking and delivery management through the following ways:
-
API Integration
The barcode system can be integrated with the company's package tracking and delivery management system through APIs. APIs (Application Programming Interfaces) allow different software applications to communicate with each other. The barcode system can be configured to send and receive data through the API, allowing it to be seamlessly integrated with other IT systems.
-
Middleware
Middleware can also be used to integrate barcode systems with other courier IT systems. Middleware software sits between the barcode system and the other IT systems, acting as a bridge between the two. This allows data to be transferred between the systems and can also provide additional functionality such as data mapping and transformation.
-
Cloud-based Solutions
Cloud-based solutions can be used to integrate barcode systems with other courier IT systems. Cloud-based solutions provide a centralized platform for different IT systems to communicate with each other. This allows the barcode system to be easily integrated with other IT systems by simply connecting to the cloud-based platform.
-
Custom Integration
In some cases, custom integration may be required to integrate barcode systems with other courier IT systems. This involves developing custom software to connect the barcode system with the other IT systems. Custom integration can be more complex and expensive than other integration methods, but may be necessary in some situations.
Overall, integrating barcode systems with other courier IT systems can improve efficiency and accuracy in package tracking and delivery management.
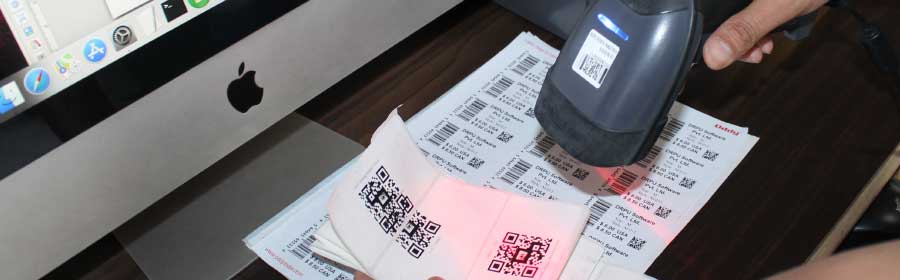
Courier company barcode systems are commonly used to track the location of packages throughout the delivery process. Each package is assigned a unique barcode that contains information such as the recipient's address, tracking number, and delivery status. The barcode is scanned at various points in the delivery process, such as when the package is picked up, when it arrives at a distribution center, and when it is delivered to the recipient.
By tracking the location and status of each package using barcode technology, courier companies can provide more accurate delivery estimates to their customers, as well as improve their operational efficiency by optimizing delivery routes and identifying potential delays or issues in real-time. Additionally, customers can use the tracking information provided by the courier company to monitor the progress of their package and plan for its arrival.
Regulatory Requirements for Courier Company Barcode Systems
Courier companies use barcodes to track and manage packages as they move through the delivery process. The regulatory requirements for courier company barcode systems can vary depending on the country and region in which they are being used.
In the United States, the Postal Service sets standards for barcode systems used by courier companies that are operating under its jurisdiction. The Postal Service requires courier companies to use Intelligent Mail barcodes (IMb) to track packages and provide delivery information. The IMb barcode must meet specific requirements for format and content.
In Europe, the International Post Corporation (IPC) sets standards for barcode systems used by courier companies that are members of the organization. The IPC requires courier companies to use the International Postal Barcode (IPB) to track packages and provide delivery information. The IPB barcode must meet specific requirements for format and content.
Other industry organizations, such as GS1, also set standards for barcode systems used by courier companies. GS1 has established standards for the use of barcodes in the supply chain, including the GS1 Logistics Label, which is used to identify and track packages as they move through the delivery process.
Overall, the regulatory requirements for courier company barcode systems are designed to ensure that packages are tracked and managed efficiently and accurately throughout the delivery process. These standards are typically set by industry organizations, such as the Postal Service, IPC, and GS1, in consultation with government agencies and other stakeholders.
Future of Barcode Technology in the Courier Industry
The future of barcode technology in the courier industry is expected to see significant growth and development, with several advancements that will improve package delivery in several ways:
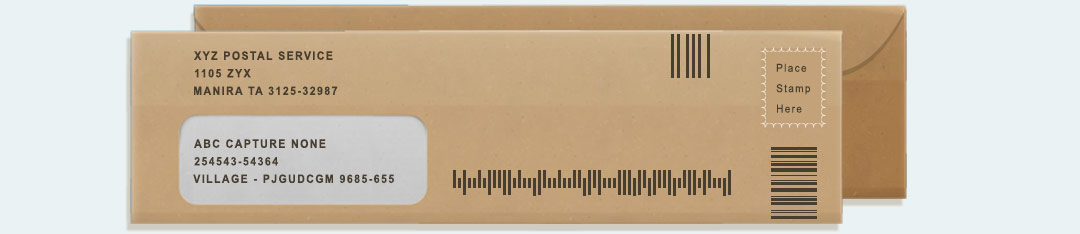
-
Improved Tracking and Visibility
Barcode technology will continue to play a critical role in improving tracking and visibility of packages throughout the courier industry. This will help customers to track their packages in real-time, leading to increased transparency and reliability.
-
Faster Delivery Times
Barcode technology can help improve delivery times by optimizing logistics, improving package routing, and reducing the chances of lost or misplaced packages. This can be achieved by using barcode scanners to quickly and accurately sort and route packages to their final destinations.
-
Increased Automation
Barcode technology can be integrated with customer service platforms, enabling customers to access real-time information about the status of their packages. This can include delivery times, locations, and any potential delays or issues.
-
Improved Accuracy and Reliability
With advancements in barcode technology, we can expect to see even greater accuracy and reliability in package tracking and delivery, further reducing the likelihood of errors and misdeliveries.