Implementing barcode systems in industrial settings can provide several benefits such as increased productivity, reduced errors, and improved inventory management. However, there are some common challenges associated with implementing barcode systems in industrial settings, which include: DOWNLOAD
-
Harsh Environments:
Industrial settings can be harsh, with high temperatures, humidity, and exposure to chemicals. These conditions can affect the quality of the barcodes, making them difficult to read. To address this issue, it is important to use industrial-grade barcode printers and scanners that are designed to withstand harsh environments.
-
Labeling Materials:
Different industrial products require different labeling materials, and these materials can affect the quality of the barcodes. To address this issue, it is important to choose the appropriate labeling materials for the products, taking into account factors such as adhesion, durability, and resistance to chemicals.
-
Barcode Size:
Industrial products can be of different sizes, and this can affect the size of the barcodes. Small products may require smaller barcodes, which can be difficult to read. To address this issue, it is important to choose the appropriate barcode size for each product and ensure that the barcode is clear and legible.
-
System Integration:
Barcode systems may need to be integrated with existing systems such as enterprise resource planning (ERP) or manufacturing execution systems (MES).
-
Cost:
Barcode systems require trained personnel to operate and maintain them. Providing adequate training to the staff is essential to ensure the system's smooth operation and to minimize errors. Implementing barcode systems can be expensive, especially for small businesses. To address this issue, it is important to evaluate the benefits and costs of the system and determine if it is cost-effective.
-
Barcode Quality:
Poor barcode quality can lead to errors in scanning, which can affect the accuracy of the system. To address this issue, it is important to ensure that the barcodes are printed correctly and that the printer is well-maintained. It is also essential to use high-quality barcode scanners that can read barcodes even if they are damaged.
-
Real-time Data:
In industrial automation, real-time data is critical for accurate decision-making. Barcode systems need to provide real-time data, which can be challenging due to network latency or system overload. To address this issue, it is important to use high-speed networks and ensure that the system is designed for real-time data transfer.
-
Security:
Barcode systems can be vulnerable to security threats such as data breaches or unauthorized access. To address this issue, it is important to implement security measures such as authentication, encryption, and access control.
-
Data Accuracy:
Barcode systems rely on accurate data, and errors in data can lead to errors in the system. To address this issue, it is important to ensure that the data is accurate and up-to-date, and that the barcode system is well-integrated with other systems such as inventory management systems or production control systems.
In summary, implementing barcode systems in industrial settings can provide several benefits but can also be challenging. Addressing these challenges requires a comprehensive approach that involves ensuring barcode quality, choosing appropriate labeling materials and sizes, integrating systems, providing adequate training, and evaluating costs.
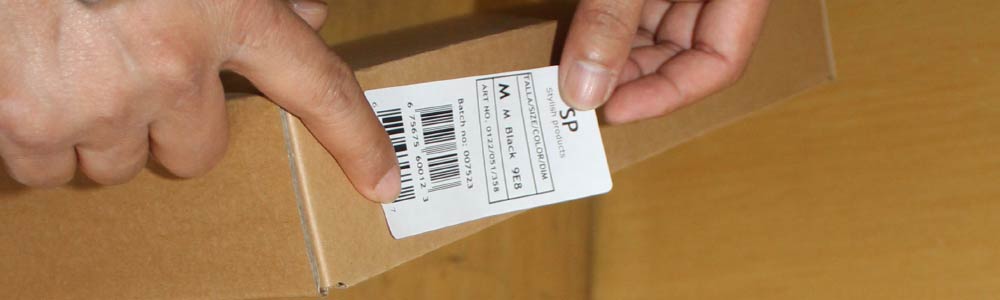
Workers Training to Use Barcode Scanning Systems in Industrial Applications
Training workers to use barcode scanning systems effectively and efficiently in industrial applications can involve the following steps:
-
Identify Training Needs
Analyze the job requirements and identify the specific tasks where barcode scanning systems are used. This will help to develop training programs that address the specific needs of the workers.
-
Provide Clear Instructions
Provide clear and concise instructions on how to use the barcode scanning system. This should include the basics of how to scan barcodes, how to interpret the information, and how to navigate the system.
-
Hands-On Training
Provide hands-on training to allow workers to practice using the barcode scanning system in a controlled environment. This can include simulated scenarios or actual scenarios in a live industrial environment.
-
Use Visual Aids
Use visual aids such as videos or diagrams to demonstrate how to use the barcode scanning system effectively. This can help workers to understand the process more easily.
-
Provide Feedback
Provide regular feedback to workers to help them improve their skills and correct any mistakes they may be making. This can help to reinforce good habits and correct bad ones.
-
Make It a Part of the Job
Integrate the use of the barcode scanning system into workers' daily tasks to encourage them to use it regularly. This can help to reinforce their training and help them to become more proficient over time.
-
Continuous Learning
Encourage workers to continue learning and improving their skills through ongoing training sessions or access to online resources.
By following these steps, workers can be trained to use barcode scanning systems effectively and efficiently in industrial applications. This can help to improve productivity, accuracy, and overall efficiency in the workplace.
Industrial Barcode Systems Integrated with Manufacturing and Inventory Management
The Integration of Barcode Systems with other industrial IT systems can help to improve efficiency, reduce errors, and provide real-time visibility into inventory and production processes. Industrial barcode systems can be integrated with other industrial IT systems through various methods such as:
- 01 Barcode Label Software:
Barcode label software can be used to create barcode labels that are compatible with other industrial IT systems and manufacturing. These barcode labels can be used to identify and track products or throughout the manufacturing process and supply chain process.
- 02 APIs:
Application Programming Interfaces (APIs) can be used to integrate barcode systems with other industrial IT systems. APIs provide a way for software applications to communicate with each other, and therefore, can be used to connect barcode systems with other systems.
- 03 Middleware:
Middleware is software that sits between the barcode system and other systems, enabling them to communicate with each other. Middleware can help to integrate barcode systems with other industrial IT systems, such as manufacturing and inventory management.
- 04 Enterprise Resource Planning (ERP) Systems:
ERP systems are software systems that are used to manage a company's resources, including manufacturing, inventory, and supply chain. Barcode systems can be integrated with ERP systems to improve inventory management, manufacturing efficiency, and supply chain visibility.
- 05 Warehouse Management Systems (WMS):
Barcode systems can be integrated with WMS to improve warehouse efficiency and inventory management. WMS can help to track products as they move through the warehouse, from receiving to shipping, and provide real-time visibility into inventory levels.
Integrated with Logistics and Inventory Management
-
Moreover, the use of cloud-based solutions can facilitate integration between different IT systems, including barcode systems. The barcode data can be stored on the cloud and accessed by other systems, enabling real-time data sharing and analysis.
-
It's essential to consider the specific needs of the industrial environment when integrating barcode systems with other IT systems. A comprehensive analysis of the existing IT infrastructure and the barcode system's capabilities is necessary to determine the most effective integration approach.
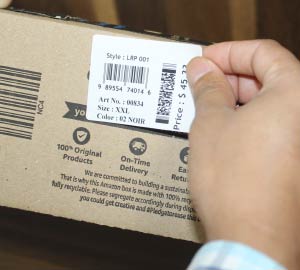
Download and Install Barcode Software for Industrial Purpose
Industrial barcode systems can be integrated with other industrial IT systems such as inventory management and logistics through various means. One common way is through the use of an Enterprise Resource Planning (ERP) system, which integrates different aspects of a company's operations, including inventory management, production, and logistics. The barcode system can be integrated into the ERP system, allowing for seamless tracking and management of inventory and logistics processes.
Another way to integrate barcode systems with other industrial IT systems is through the use of Application Programming Interfaces (APIs) that enable communication between different software systems. For example, the barcode system can be connected to a warehouse management system or a transportation management system through APIs, allowing for real-time tracking and monitoring of inventory and logistics operations.
Posted By: Teachable Tech | Last Updated On: