Accuracy and Quality of The Information Encoded in Barcodes
Shipping workers can ensure the accuracy and quality of the information encoded in barcodes by following these steps:
- Verify That the Barcode Label is Properly Printed and Readable: Workers should check that the barcode is printed correctly and clearly visible. They can use a barcode scanner to verify that the label can be read.
- Ensure That the Barcode Label Matches the Item Being Shipped: Workers should match the barcode label to the item being shipped to ensure that the correct label is attached to the correct item.
- Check That the Information Encoded in the Barcode is Accurate: Workers should verify that the information encoded in the barcode matches the information on the shipping documentation.
- Perform Regular Checks and Audits: Workers should regularly check and audit the barcode system to ensure that it is functioning correctly and that the data being encoded is accurate.
By following these steps, shipping workers can ensure the accuracy and quality of the information encoded in barcodes, which can help to improve the efficiency and reliability of the shipping process.
Improved Efficiency and Accuracy in The Processing and Delivery of Packages
Shipping barcode systems improve efficiency and accuracy in the processing and delivery of packages and freight in several ways:
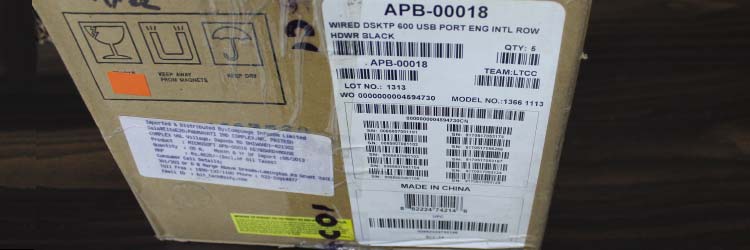
-
Real-time Tracking: Barcode systems allow for real-time tracking of packages and freight, giving shipping companies and customers accurate and up-to-date information on the location and status of their shipments. By scanning the barcode at each stage of the shipping process, the system can provide real-time tracking information to the sender and recipient. This helps to reduce the number of lost or misplaced packages and provides customers with greater visibility into the delivery process.
-
Inventory Management: Barcode systems can also be used to manage inventory and track the movement of goods within a warehouse or shipping facility. By scanning barcodes on incoming and outgoing packages, the system can maintain an accurate inventory count and ensure that the correct items are shipped to the correct destination.
-
Quick and Accurate Scanning: When a package arrives at a shipping facility, the barcode on the package is scanned by a barcode scanner. This allows the system to quickly identify the package and access its information, such as the recipient's address, shipping method, and package weight.
-
Reduced Labour Costs: Barcode systems can reduce labour costs by eliminating the need for manual data entry and reducing the number of errors and miscommunications that can occur in manual processes.
-
Faster Data Entry: With barcode scanning, package information is quickly and accurately entered into the system. Scanning barcodes can be up to 20 times faster than manual data entry.
-
Improved Customer Service: With real-time tracking information and accurate delivery estimates, customers can have a better experience and greater confidence in the shipping process.
-
Improved Accuracy: Barcode scanners eliminate the potential for human error in data entry, ensuring that package information is accurate and up-to-date.
-
Automatic Sorting: Barcode systems can also be used to sort packages automatically, based on their destination or shipping method. This can save time and reduce errors compared to manual sorting, which can be time-consuming and error-prone.
Overall, shipping barcode systems help to improve efficiency, accuracy, and transparency in the shipping and delivery process, which can lead to faster delivery times, improved customer satisfaction, and reduced costs for shipping companies.
Improved Package Tracking and Delivery Management
- Shipping barcode systems improve package tracking and delivery management by providing a unique identifier for each package that is scanned at different points in the shipping process. As a package moves through the shipping process, the barcode is scanned at different checkpoints, such as when it is picked up, when it arrives at a sorting facility, when it is loaded onto a truck or plane, and when it is delivered to the final destination.
- This information is then fed into a centralized tracking system, which allows shippers and recipients to track the progress of the package in real-time. Shipping barcode systems can also improve delivery management by providing route optimization and scheduling tools, as well as real-time alerts and notifications to drivers and customers about the status of their shipments. Overall, shipping barcode systems can help to streamline the shipping process, reduce errors and delays, and improve customer satisfaction.